La flotación de espuma es la manera mediante la cual los minerales liberados en la sección de molienda se separan en fracciones valiosas y no valiosas. Desde su primera aplicación comercial en una mina de zinc en Australia en 1905, la flotación se ha vuelto cada vez más importante como un método de recuperación de minerales. En la actualidad es un proceso esencial para recuperar una amplia variedad de minerales metálicos (plomo, zinc, níquel, cobre, molibdeno, etc.) y minerales no metálicos (barita, calcita, grafito, arenas silíceas, potasa, talco, etc.).
La flotación tiene lugar en recipientes llamados celdas de flotación. La flotación depende de las capacidades de los diferentes minerales para adherirse a las burbujas de aire formadas en una pulpa. En el proceso de flotación, se hace ascender burbujas de aire a través de la pulpa y formar una espuma sobre la superficie de la celda de flotación. Se agregan químicos (reactivos) a la pulpa para ayudar en la formación del tipo correcto de espuma. Pequeñas cantidades de otros químicos reactivos hacen que algunos minerales (pero no otros) se adhieran a las burbujas de aire y suban a la superficie de la celda de flotación. Generalmente, se hace que los minerales valiosos se adhieran a las burbujas, mientras que las partículas de mineral estéril (ganga) permanecen en la pulpa.
La superficie mineral tratada químicamente se denomina superficie hidrófoba. Esto significa que la superficie es atraída al aire y es repelente al agua. Por lo tanto, las partículas minerales tratadas con un reactivo colector son atraídas a las burbujas de aire en la espuma, y cuando hacen contacto, el colector adhiere el mineral valioso a la burbuja de aire. Esto hace que los minerales valiosos suban a la superficie de la celda de flotación con las burbujas de aire.
Los minerales remanentes humedecidos por el agua que no son atraídos ni se adhieren a las burbujas de aire se denominan hidrófilos. Esto significa que son atraídos al agua y no al aire. No suben a la superficie de la celda de flotación y no se incluyen en la espuma.
Luego, la espuma es despumada para completar la separación. La espuma se denomina concentrado, y la pulpa remanente se denomina relaves o colas. La fotografía abajo muestra la espuma que se forma en una celda de flotación típica. Advierta la acumulación, o coalescencia, de las burbujas de aire.
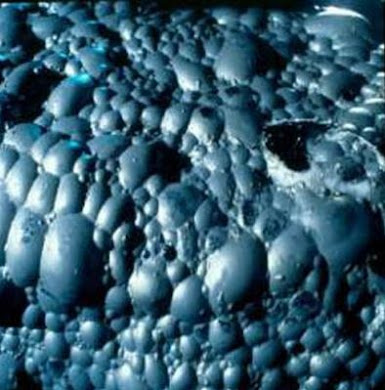 |
Fig.1 Espuma de celda de flotación-contenido concentrado |
ETAPAS DE FLOTACIONPara mejorar la eficiencia del proceso de flotación normalmente se usan varias etapas de flotación. Las etapas comúnmente empleadas son las etapas de flotación primaria, limpieza y barrido.
La etapa de flotación primaria trata la alimentación entrante del circuito de molienda y opera para obtener la recuperación máxima. El concentrado primario de esta etapa es de baja ley.
La etapa de limpieza recibe el concentrado primario como alimentación. Las condiciones cambian para producir una ley tan alta como sea posible. La ganga es rechazada del concentrado en los limpiadores y sale del circuito como relaves de las celdas de limpieza. En ocasiones, se requiere de varias etapas de limpieza, con el concentrado del primer limpiador siendo la alimentación del segundo limpiador y así sucesivamente. En cada etapa consecutiva, el concentrado aumenta más y más su ley, y se rechaza más ganga.
La etapa de barrido recibe los relaves de la etapa de flotación primaria. El concentrado del barrido generalmente es de muy baja ley y habitualmente se limpia bajo condiciones distintas a las del concentrado primario de flotación más rápida. De la misma manera, los relaves de la etapa de limpieza generalmente contienen una cantidad significativa de mineral valioso y ellos también son barridos antes de su rechazo final desde la planta. El barrido de relaves de la etapa de limpieza se conoce como etapa de limpieza y barrido o simplemente como etapa de barredores limpiadores.
CELDAS DE FLOTACION :CELDAS DE ESTANQUE
Hay varios diseños de celdas de flotación. La mayoría de los nuevos concentradores usan celdas de estanque cilíndrico para la etapa de flotación primaria. Otro tipo de celda usada es la celda convencional. Las celdas convencionales son rectangulares en vista en planta y se describen en la subsección siguiente. Las celdas de estanque son más grandes que las celdas convencionales y son en realidad estanques que contienen un agitador o rotor. El rotor de la celda de flotación promueve la suspensión de sólidos y la dispersión del aire dentro de la pulpa. Por ejemplo, Outokumpu es un fabricante que produce celdas de estanque. Para producir burbujas y contactar las burbujas con la pulpa, las celdas de flotación Outokumpu usan un rotor y un estator para mezclar completamente los componentes sólidos y líquidos de la pulpa.
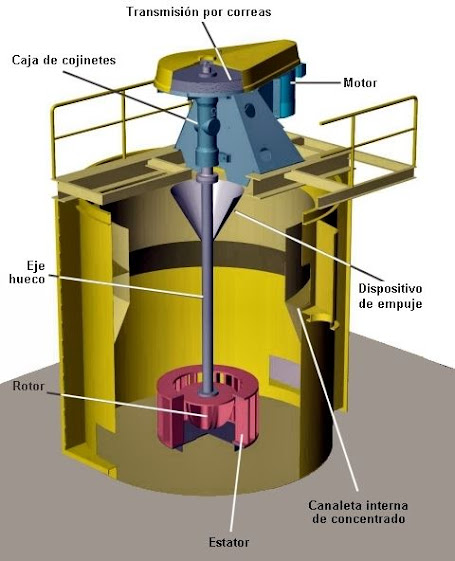 |
Fig.2 Celdas de estanque |
El rotor en la celda Outokumpu tiene forma de estrella y es redondeado en los bordes. Se introduce aire dentro de la pulpa a través del eje hueco conectado al rotor y mecanismo de accionamiento. El mecanismo de accionamiento del rotor está compuesto de un motor conectado al eje del rotor mediante correas en V y poleas acanaladas. El motor acciona el eje del rotor. Un soplador de aire de baja presión suministra aire dentro del eje. Una válvula de control de flujo de aire automática ajusta el flujo de aire sobre la base de la lectura de un indicador de flujo de aire.
La acción mezcladora del rotor y estator crea zonas dentro de la celda de flotación: una zona de circulación de pulpa, una zona de mezclado de aire y pulpa, una zona de separación y una región de espuma superior.
 |
Fig.3 Acción al interior de una celda de flotación |
La acción de bombeo del rotor impulsa la pulpa desde el fondo de la celda, hacia arriba a través del estator, y dentro de la celda. A medida que el rotor desplaza la pulpa, el aire proveniente del soplador externo se alimenta uniformemente dentro del flujo de pulpa a través de ranuras verticales en el rotor. Mientras el aire y la pulpa pasan a través del estator, el aire se dispersa como finas burbujas. Las burbujas creadas en la zona de mezclado suben a la parte superior de la celda, llevando minerales valiosos. La forma cilíndrica del estanque mejora la dispersión del aire. Se forma espuma, de varios centímetros de profundidad, en la parte superior de la celda. Contiene minerales valiosos, pero también algo de ganga atrapada entre las burbujas.
Parte de esta ganga tiene la oportunidad de caer de vuelta dentro de la pulpa a medida que el agua drena de la espuma, pero gran parte de ella se mantiene en la espuma. Hay una placa de empuje, en forma de cono invertido, fijada a la parte superior de la celda. La placa de empuje mejora el transporte de espuma hacia la canaleta recolectora forzando la espuma hacia la canaleta circular interior en la celda.
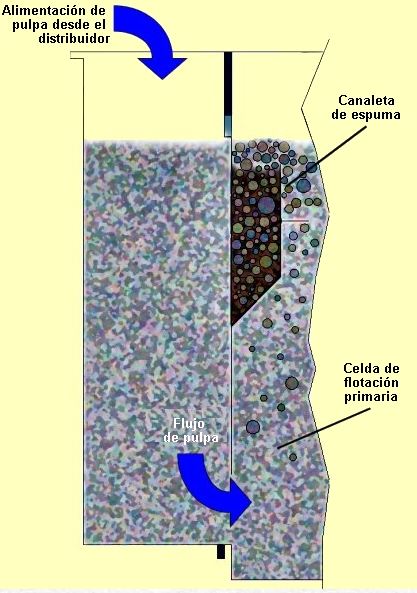 |
Fig4. Canaleta de espuma en una celda de flotación |
La espuma fluye sobre el reborde de la canaleta circular interior en la celda. La canaleta se muestra en el diagrama en corte arriba. La canaleta está inclinada y la espuma fluye por la pendiente hacia una tubería de descarga.
Para lograr una recuperación aceptable de un mineral, debe permitirse un tiempo de retención suficiente para todos los minerales que vayan a ser flotados. Bajo altos caudales de mineral, se hace necesaria la presencia de más de una celda para lograr la recuperación deseada y evitar cortocircuitar los valores minerales. En un proceso continuo, las celdas de flotación se disponen en bancos para agregar tiempo de retención. Al estar configuradas en un circuito, con dos o más celdas conectadas secuencialmente, el grupo de celdas se conoce como un banco.
Cada celda en un banco está conectada mediante cajones de transición. La pulpa fluye secuencialmente a través de todas las celdas en el banco. Los bancos reciben alimentación a través de un cajón de alimentación y se unen mediante cajones de unión conectores o intermedios. La pulpa sale de la última celda en el banco a través de un cajón de descarga o relaves. Para dejar la última celda, la pulpa debe pasar a través de válvulas de dardo que controlan el nivel en cada grupo de dos celdas.
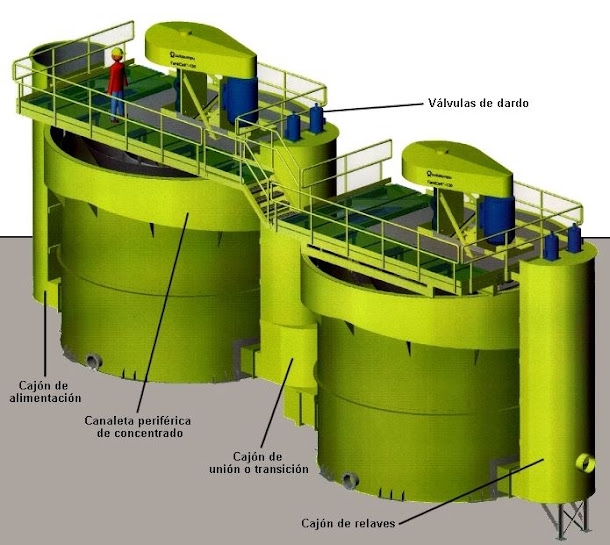 |
Fig.5 Bancos de celdas |
Los cajones de conexión, uniendo la celda o grupos de celdas entre sí, también tienen válvulas de dardo. Una válvula de dardo se muestra en la fotografía arriba y en el diagrama abajo.
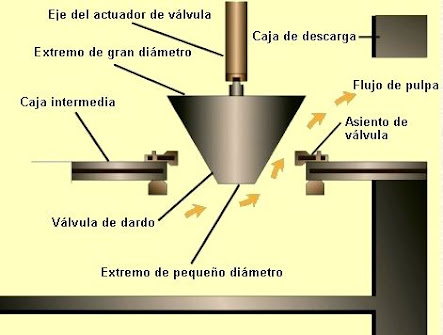 |
Fig 6. Diagrama esquemático y partes de válvula tipo dardo
|
La pulpa fluye dentro del cajón de alimentación de la primera celda en el banco. Luego fluye hacia el fondo del cajón de alimentación e ingresa al fondo de la primera celda. El nivel de pulpa se controla automáticamente mediante el ajuste de las válvulas de dardo en el extremo de descarga de la celda. El cambio de abertura de la válvula de dardo ajusta el flujo de pulpa liberado desde la celda. De esta manera, se mantiene el nivel de pulpa deseado en la celda. Este proceso continúa a lo largo de cada celda en el banco hasta que la pulpa descarga por gravedad dentro del cajón de relaves.
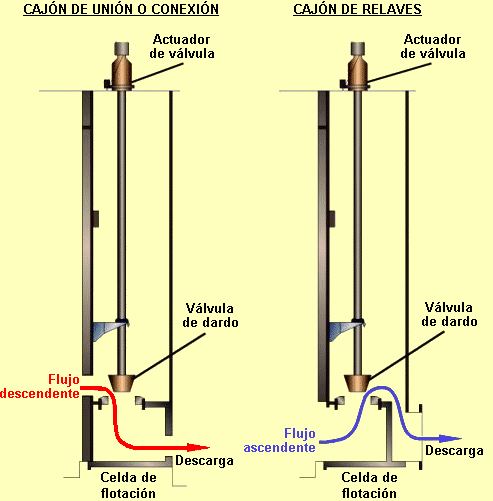 |
Fig.7 Disposición de válvula de dardo |
El diagrama arriba ilustra la disposición de la válvula de dardo tanto en el cajón de conexión como en el cajón de relaves. La disposición de la válvula de dardo en el cajón de unión o conexión permite que la pulpa fluya hacia abajo a través de la válvula de dardo. La disposición de la válvula de dardo en el cajón de relaves permite que la pulpa fluya hacia arriba a través de la válvula de dardo.
Advierta que a medida que el nivel de pulpa en la celda de flotación aumenta, la cantidad de espuma disminuye, ya que más de ésta es despumada dentro de la canaleta de concentrado. En forma inversa, a medida que el nivel de pulpa disminuye, la cantidad de espuma aumenta, ya que menos de ésta es despumada dentro de la canaleta de concentrado. El diagrama abajo ilustra este efecto.
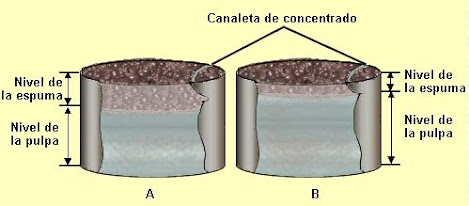 |
Fig 8. Representación de operación de celdas |